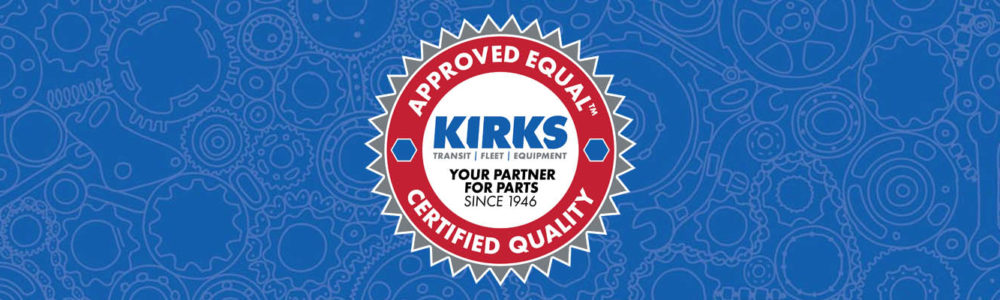
Considering Aftermarket Parts Options for Fleet and Transit Maintenance: OEM, Third-Party, or Repair?
Technicians and maintenance managers face many daily hurdles to keep their vehicles in good running condition, and sourcing quality parts is often the biggest challenge. Balancing budget demands against the need for available quality parts with prompt turnaround can be a frustrating, repetitive burden.
What are the options available when seeking transit and fleet replacement parts? The most commonly considered sources for parts are either direct OEM parts, third-party replacement parts or repaired parts. We’ll cover these options and how the KIRKS’ Approved Equal™ seal of quality changes the aftermarket parts landscape.
OEM Parts – Quality for a Price
Original Equipment Manufacturer (OEM) parts, as the name suggests, come straight from your vehicle’s original manufacturer or dealer. The same factory that made your old, broken part supplies your new, shiny part. These parts set the standard, but they come at a premium cost.
- Pro: OEM Parts promise security. Your OEM replacement parts often ensure high quality, reliability, and proper fitment. Your maintenance team can readily install these parts, knowing that they are made specifically for the application and will function appropriately.
- Con: OEM Parts are the most expensive option. OEM parts have high price markups, making them costly. These higher supply costs put pressure on fixed budgets and force dilemma decisions, leaving little room for other essential expenditures.
- Con: Warranty Pressure. OEMs can propose to wave the warranty banner on new vehicles to pressure teams toward brand loyalty. The message communicates that purchasing a part from a third-party source will void a vehicle’s warranty: this is a threat many fall victim to.
- Con: OEM Parts are not always the standard of quality! When OEMs provide newly developed and marketed parts, unknown weaknesses can surface. At times, we’ve seen OEM parts disappoint in quality, and the OEMs are slow to provide solutions for defects in parts. Since we work closely with our customers, we learn about OEM parts defects early. The KIRKS team embraces these challenges: we innovate solutions well before the OEM can respond.
Third-Party Replacement Parts
Third-party replacements, commonly referred to as aftermarket replacement parts, are manufactured by someone other than the OEM. There are many manufacturers in the automotive industry that reverse engineer the original OEM design. These sources provide an alternative product that typically drops right into your application.
- Pro: Aftermarket Parts are cheaper than OEM parts. Aftermarket parts are usually a significantly more affordable alternative to the OEM. In many instances, they can be as much as 50% cheaper, primarily because aftermarket manufacturers don’t bear the burden of development costs and overhead associated with being an OEM.
- Pro: Rule the Aftermarket. Many OEM part manufacturers are so focused on serving their primary customers: the vehicle, bus, or equipment manufacturers, that they ignore and underserve the aftermarket. Their customer service to end-users is often either woefully understaffed or completely non-existent.
However, these are aftermarket manufacturers’ customers and are solely focused on serving these end-users. Aftermarket manufacturers range in quality of customer service. Those who provide better post-sales support better understand real-world issues and the problems facing the industry.
- Con: Do you know what you’re getting? There can be a risk associated with using a non-OEM part when you don’t have confidence in your supplier. Are the quality and reliability equal or better than the OEM? Will the part fit your application without issue? These questions are hard to answer if you don’t have much information about the aftermarket manufacturer.
There are many cheap aftermarket manufacturers in the marketplace with unreliable parts. Navigating this arena can be difficult without a deep knowledge of the industry and a well-established relationship with quality third-party manufacturers.
Aftermarket Repairs – Savings at the High Cost of Quality
Many repair vendors promise to offer the repaired part you need at a lower cost, but many fear they’re taking a risk. Every shop has stories about receiving repaired parts that were defective and created more of a hassle than the part was worth. We’ve heard these stories and have seen them firsthand.
A KIRKS FLASHBACK:
“A few years back, I was at the local transit authority, running a demonstration for the technicians on a new emissions system, when they received a part from another supplier. We couldn’t believe our eyes: it was a mess when they pulled it out of the box. It even had oil dripping and was completely unusable. Sending such a messed-up part seemed flat-out disrespectful, and I felt bad for the crew. (It worked out OK in the end, I was able to get them an Approved Equal replacement, same day!)”
– Mike Smith, KIRKS Production Manager
There are no licenses or governing regulations overseeing the repairs from third-party companies. Standards vary, testing is inconsistent, and specifications may differ from an OEM.
- Pro: Lower cost. Repair vendors often offer lower-priced parts, allowing you to stay on budget and keep your vehicles moving.
- Con: Quality is not guaranteed. You can never have total confidence because there are different standards. This can mean the parts don’t work as expected, don’t fit the application, don’t meet quality standards, or just don’t last.
- Con: Inferior parts increase their cost. It’s a risk that shops feel they have to take to save money but instead end up buying more parts, more often, with more fleet downtime and higher labor costs.
Approved Equal™ Seal of Quality for Parts – Proven Quality and Affordable Cost
Recognizing that neither OEM parts nor third-party suppliers provided the confidence that fleet and transit managers needed, KIRKS sought to create a solution. Aftermarket parts are often a preferred option over OEM replacement parts, and many can even out-perform the OEMs. But how can buyers be sure that they won’t purchase defective or inferior third-party or repaired parts? Maintenance technicians must be confident that the parts they buy are proven to meet or exceed OEM standards. The Approved Equal™ Seal of Quality provides that assurance.
- Pro: Quality Assured. KIRKS’ Approved Equal™ Seal of Quality is only placed on parts proven to meet or exceed OEM performance specifications. This also applies to KIRKS remanufactured parts, following a strict, controlled manufacturing process and are functionally tested to meet the exact OEM specifications.
- Pro: Non-OEM Confidence. We vet suppliers who qualify for our Approved Equal™ Seal of quality through KIRKS’ national distribution networks. Buyers are never left wondering about reliability.
- Pro: Right Priced. Approved Equal™ parts are available at a significantly lower cost than OEM parts. Shops stay on budget, keep their fleets moving, and escape the parts trap!
- Bonus: Remanufacturing is environmentally friendly. Reusing non-critical hard parts without sacrificing quality is a win-win, replacing new part production processes to reduce industrial waste.
How does Approved Equal work? – Our Proven Process
KIRKS Approved Equal™ means the product you purchase will meet or exceed OEM standards for performance and reliability, offering the parts solution that fleet and transit professionals need. The engineering and purchasing teams at KIRKS review each part and application. They scrutinize prints, drawings, specifications, and test results to ensure that each Approved Equal™ product meets or exceeds the OEM specifications.
Making the best in a monolithic system of aftermarket parts
Many OEMs play a game with part numbers, creating confusion, making it difficult to compare alternatives, and monopolizing aftermarket parts sourcing. We get calls from purchasing departments trying to find parts through OEMs, but their automated systems make it difficult, and phone support can be unhelpful, even intimidating. A significant part of working with our customers is helping them through the aftermarket parts maze.
Getting Past the OEM Logo
KIRKS’ Product Managers help customers identify the actual manufacturer of the needed part. KIRKS usually has a direct relationship with that manufacturer and can directly source the required part. We also routinely review our supplier’s quality systems and track warranty performance to ensure confidence and quality in every part.
KIRKS Makes it Possible
KIRKS Approved Equal™ is our solution to the parts trap that keeps maintenance teams stuck between expensive OEMs and unreliable aftermarket parts. It is our guarantee and promise that the product we source will meet or exceed OEM standards.
KIRKS employs some of the best and brightest industry experts who have been working in the transit and fleet business for decades.
Our goal is to provide innovative solutions with personal service to keep your fleet and our world moving. Approved Equal™ delivers on that promise. If you are frustrated with the cost and quality demands for your repair parts, call KIRKS. We’ll help you discover the Approved Equal™ solution to confidently keep your vehicles moving.